How Welding Inspection Madison Makes Sure High Quality and Safety in Fabrication
How Welding Inspection Madison Makes Sure High Quality and Safety in Fabrication
Blog Article
Discovering Advanced Tools and Methods for Accurate Welding Examination
In the world of welding inspection, the quest of precision and dependability is extremely important, stimulating the advancement of sophisticated devices and approaches. Technologies such as phased selection ultrasonic testing and digital radiography are changing problem discovery, offering unrivaled precision in identifying welding flaws. Additionally, laser scanning innovations and automatic examination systems, equipped with synthetic intelligence, are redefining the landscape by minimizing human mistake and enhancing security steps. As these advanced techniques remain to evolve, they promise not just to change examination practices but also to raise intriguing questions about the future of quality assurance in industrial applications.
Ultrasonic Evaluating Innovations
Ultrasonic screening innovations often stand for the center of developments in welding assessment technologies. These developments have significantly enhanced the capability to identify and evaluate gaps within bonded frameworks, making certain improved integrity and safety.
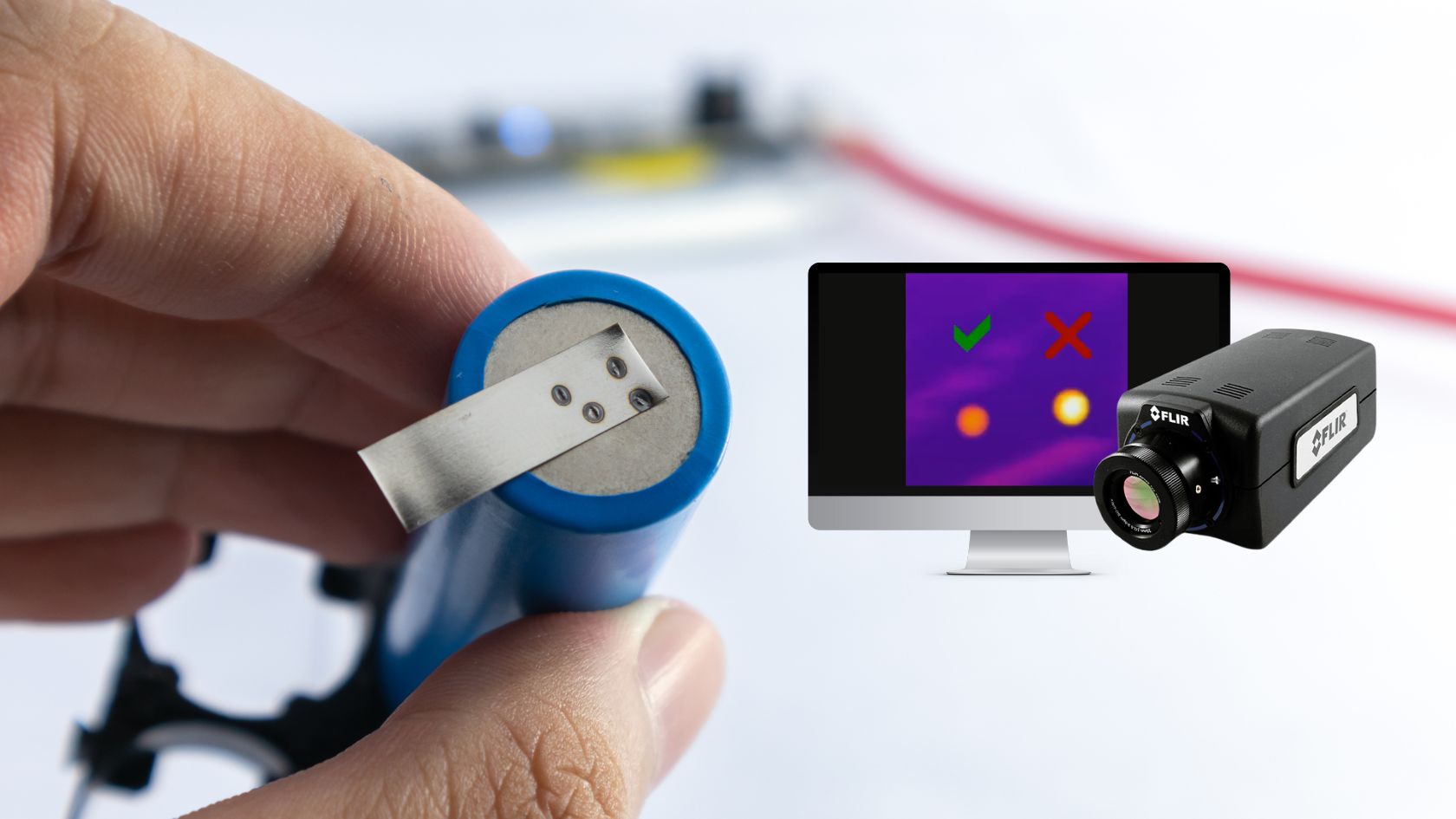
Furthermore, innovations in software algorithms for data evaluation have actually boosted the accuracy of problem detection and sizing. Automated ultrasonic screening systems currently offer high-resolution imaging, making it possible for detailed evaluations of weld top quality. These systems are frequently incorporated with advanced visualization devices, which promote the interpretation of results.
Radiographic Assessment Strategies
While ultrasonic screening innovations have set a high standard in non-destructive examination, radiographic evaluation methods proceed to play an indispensable duty in welding examination by offering unique insights into material stability. Radiographic screening (RT) uses the usage of X-rays or gamma rays to penetrate materials, producing a radiograph that visually represents the internal structure of a weld. This imaging capacity is very useful for detecting subsurface defects such as porosity, inclusions, and cracks that might not be noticeable with surface evaluations.
The process entails positioning a radiation source on one side of the weld and a detector on the opposite side. Variants in material thickness and thickness impact the attenuation of the rays, generating a different picture that precisely defines problems. RT is particularly advantageous for evaluating thick sections and complex geometries where various other methods might fail.
In spite of its effectiveness, radiographic evaluation must be performed with strict adherence to safety and security procedures due to the harmful nature of ionizing radiation. Furthermore, the analysis of radiographs requires skilled workers, as the quality of the evaluation directly influences the dependability of the inspection. Ongoing developments in electronic radiography are boosting image clearness and interpretation effectiveness, enhancing RT's critical role in making sure weld top quality.
Laser Scanning Advances
Accepting laser scanning technology in welding inspection has actually reinvented the evaluation of weld quality and honesty. Unlike standard evaluation techniques, laser scanning gives rapid information purchase, significantly boosting the effectiveness and accuracy of weld analyses.
Laser scanning developments have brought about considerable renovations in finding and defining surface problems such as porosity, lack of combination, and damages. The high-resolution data allows inspectors to do comprehensive evaluations, ensuring that welds satisfy rigorous industry requirements. Furthermore, this technique sustains the development find out this here of digital records, promoting long-term high quality guarantee and traceability.
In addition, laser scanning modern technology integrates perfectly with software solutions made for automated problem discovery and analysis. The resultant information can be conveniently shared and assessed, advertising joint decision-making procedures. As sectors remain to require greater requirements for weld high quality, laser scanning stays at the leading edge, using unmatched accuracy and performance in welding examination.
Automated Examination Equipments

Automated inspection systems offer the advantage of consistency, removing human mistake and subjectivity from the assessment procedure. They are developed to operate in numerous settings, from production floors to remote area sites, guaranteeing detailed protection. Welding Inspection read this article Madison. These systems can be programmed to comply with certain welding standards and standards, giving in-depth reports and documents for high quality control objectives
Moreover, the assimilation of cloud-based platforms facilitates the storage and evaluation of large quantities of assessment data. This allows trend evaluation and anticipating maintenance, permitting producers to resolve prospective concerns before they intensify. The fostering of automatic examination systems is a critical action towards boosting the dependability and performance of welding processes in commercial applications.
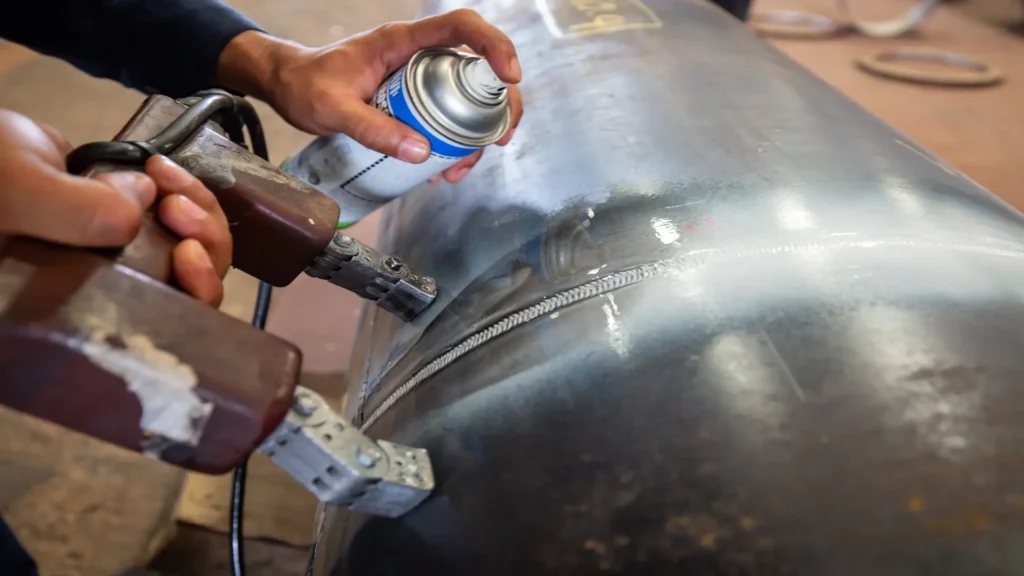
Enhancing Safety and Efficiency
A significant aspect of boosting security and effectiveness in welding assessment lies in the combination of cutting-edge modern technologies that improve operations and mitigate threats. The adoption of advanced non-destructive screening (NDT) methods, such as ultrasonic screening, phased range ultrasonic testing (PAUT), and radiographic screening, plays a pivotal duty in making sure structural honesty without compromising the safety of the employees entailed. These methods permit thorough assessments with minimal downtime, minimizing potential dangers associated with standard methods.
Moreover, the implementation of real-time data analytics and artificial intelligence algorithms has actually transformed the method examination data is translated. By using predictive analytics, prospective flaws can be identified before they materialize right into crucial failings, guaranteeing timely interventions and upkeep. This aggressive approach considerably improves functional performance and safety and security in welding processes.
In addition, remote examination modern technologies, consisting of drones and robotic spiders furnished with high-resolution additional info cams, enable inspectors to examine hard-to-reach areas without exposing them to harmful conditions. This not just enhances evaluation precision however also lessens human risk. By leveraging these innovative tools and approaches, markets can achieve greater safety criteria and operational effectiveness, ultimately causing more trusted and lasting welding inspection methods.
Conclusion
The combination of innovative tools and methods in welding evaluation substantially enhances issue discovery and ensures structural integrity. These advancements not just raise inspection performance yet additionally add to improved security and quality assurance in commercial welding applications.

Ultrasonic testing developments frequently stand for the leading edge of advancements in welding examination innovations.While ultrasonic testing innovations have actually set a high criterion in non-destructive assessment, radiographic assessment techniques proceed to play an important duty in welding examination by supplying one-of-a-kind understandings into product integrity.Welcoming laser scanning technology in welding examination has changed the evaluation of weld top quality and stability. As sectors continue to require greater requirements for weld top quality, laser scanning remains at the center, offering unmatched precision and performance in welding inspection.
Automated examination systems provide the benefit of consistency, getting rid of human mistake and subjectivity from the inspection procedure.
Report this page